

Remove the leg and rib top from the overlap rib with snips, then tab around the rib and cut flush. Use the bending tool to form a hem under the pan.Ĭut off the underlap rib completely. Make a mark one inch from the end of the panel and cut along the base of each rib with snips. The first panel is the most important panel of your installation. To prepare for installation of the first metal panel, you will need to apply sealant on the eave trim. Overlap the end a minimum of six inches when starting a new roll of underlayment.Īlso, keep in mind during the installation that areas that have been cut or torn should be replaced or repaired prior to moving on to the next step. Start the installation of the underlayment at the intersection of an eave and a gable end, and then roll it out parallel to the eave end.Īllow each consecutive course to overlap the previous one by at least four to six inches. This is especially true if you live in a cold climate. Here, you will need to use an ice and water shield. Then, carefully check the areas of the roof around chimneys, valleys or skylights. Cover the entire roof with 30-pound felt paper or titanium underlayment. You must now give your roof a layer of protection, known as the underlayment. After all the eave trims are affixed, you are ready to move on to the next step. Between any trim that overlaps, you will need to apply sealant.
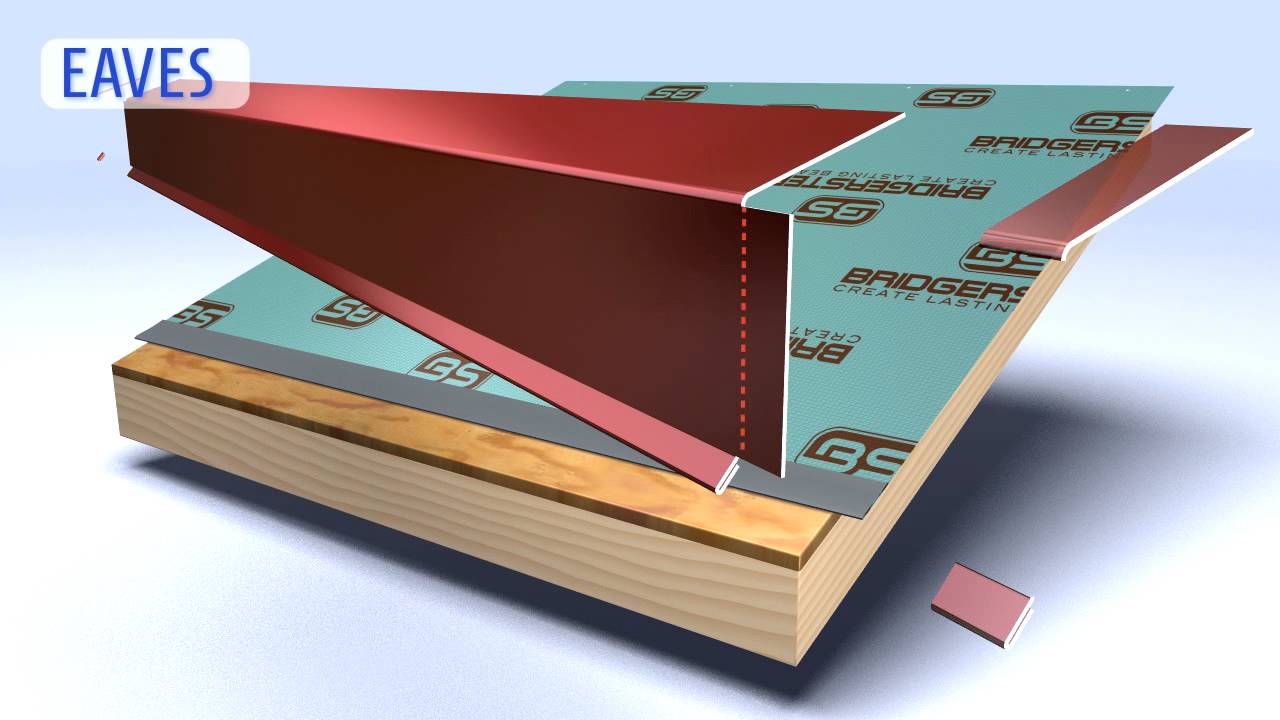
Take note of the angles being cut to allow the trim to overlap. Cut the trim as needed and attach with the appropriate roofing nails and screws. You will have to flash any two eave trims that meet.

The eave trim will then be fastened along the fascia with screws spaced 16 inches on center. Place the appropriate eave trim in line with the substrate and fasten it to the decking 18 inches on center with roofing nails. Make sure you select an eave trim that is designated as appropriate for your specific roof pitch. The first flashing to install is the eave trim. Carefully pay attention to each step and focus on your safety while up on the roof. The following steps will guide you in installing a standing seam metal roof.

This could save you a lot on shipping before installation. This is because many suppliers can make your standing seam panels according to your exact details, right there on site. If you will be installing a standing seam meal roof yourself, think about buying your metal panels from a local sheet metal roofing supplier. Sealant/ caulking (must be watertight with strong adhesion).Underlayment (must be durable and watertight).The following tools and materials will assist you in the installation of the standing seam metal roof: As a general rule of thumb, without going up on the roof, you can take the width of your home in feet, multiply this number by 12 and divide the result by 16.Īssuming each panel is 16 inches wide, this will tell you how many panels you need for installation on each side of your home. Once you have the roof measurements, you’ll know how many panels are required for the installation. The typical standing seam drip edge extends 1 inch beyond the eave, and then it gets bent back by an inch. These extra 2 inches will later form the drip edge hem, so it’s important to have this extra length for each panel. You need to measure the vertical run from the eave of the roof all the way to the ridge line and then add in another extra two inches. Each measurement needs to be exact to the inch. You need to take special note here: if the panels are too short, they will be unusable, so you must measure them carefully. You will need to measure your roof – including every eave, gable, ridge, valley and side wall – in order to ensure that you buy the right size roof panels. Not only that, but also the granular surface of the asphalt shingles can rub up against the metal panels, potentially causing them to rust from underneath.
